クリーンルーム内で稼働するリフターのシェア90%
半導体製造を陰で支えるナンバー1企業
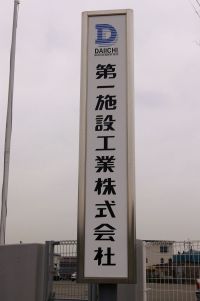
半導体の大家も思わずうなった
第一施設工業の非接触搬送技術
「こういう方法があったのか。これは気付かなかった」
東北大学工学部・大見忠弘教授は第一施設工業の非接触搬送装置を目の当たりにして思わずうなった。
東北大学の大見忠弘といえば日本の、いや世界の半導体業界でも知らぬ人がいないくらいの有名人である。大学教授でありながら700件を超える特許を出願しているし、東北大学のスーパークリーンルーム建設委員長を務めたこともある。というより、「インテルを立ち直らせた男」としての方が知られているだろう。
87年に大見が発表したスーパークリーンルームに関する論文を見たインテルが、指導を受けたいと大見本人を本社に招待し、レクチャーを受けたのは有名な話だ。
当時、アメリカの半導体製造は不良率が高く、歩留まり20〜30%というのが一般的だった。ところが大見の指導の下、クリーンルームを建設し直したインテルの半導体は歩留まり率が85%に改善されたのだ。もし、この時大見のレクチャーを受けなかったら、恐らく現在のインテルはなかったに違いない。
そこまで半導体製造に関することを知り尽くした大見が、第一施設工業の非接触搬送装置を見て感心したのである。
実は、大見は以前、篠原から相談を受けたことがあった。
「非接触? あれはダメだ。やめておけ」
大見は「非接触」と聞いて、即座にそう答えたのだ。
「自分も非接触はやってみたがダメだ。あれは使い物にならない」
半導体の大家からそう言われれば普通は諦めるところである。しかし、逆に篠原はその一言にファイトを燃やしたのだった。
公開特許からヒントを得て
非接触搬送装置を自社開発
現在、クリーンルーム内での搬送はウエハーや液晶パネルの元になる液晶ガラス基板をローラーコンベヤーの上に水平に置き移動させる方法である。
ところが、この方法だとウェハーや液晶ガラス基板が大型化すればするほどコンベヤーの幅を広くしなければならない。いきおいガラス基板等を支える支持点も増えてくる。支持点が増えれば汚れが付着する箇所も増える。
また、ガラス基板が大型化すればガラス基板自身の重みでたゆみができる。第7世代といわれる1870o×2200oサイズの液晶ガラス基板ともなれば中央部が10p近くもたゆんで下がってくる。すると、そこに洗浄液が残ったり、ちょっとした接触で割れたりする。いずれにしろ不良品が出やすくなる。
このように半導体業界は基板の大型化に伴うロスをいかに減少するかという新たな課題を抱えていた。篠原もクリーンルーム内の搬送装置メーカーとして、この課題を解決すべき方法を模索していた。
そんなある日、福岡県内の未利用特許を紹介した冊子を何気なくめくっていた篠原の手があるページでピタッと止まった。「板状体の無接触搬送技術」と書かれた文字で目が止まった。
無接触? 初めて目にする文字だった。詳しい内容は分からなかった。が、篠原はその言葉に大いに興味を持った。
「もしかすると使えるかもしれない」
早速、その特許技術を公開した県内企業に連絡を取り、その使用権を得た。
原理は上からワークに向かって空気を噴出し、ベルヌーイの効果でワークの上に負圧が発生するのと、ワークの下にエアクッションができるのを利用してワークを浮き上がらせる方法である。
ところが、実際にやってみると色々問題が出てきた。
クリーンルーム内は、ダウンフローといって常に上から下へ秒速30pのエアーがゆっくり流れている。このダウンフローで空中のミクロン単位の塵埃を床下に排除し、室内をクリーンに保っているのだ。そこに強力なエアーを噴出させれば今まで一定の速度で流れていた気流に乱れが生じ、逆に塵埃を巻き上げてしまう。
「だめだ、これは使えない」
面白いと思った非接触搬送だったが、実用化は無理だった。研究チームの中に諦めムードが漂いだした。それでも篠原は非接触にこだわった。
浮上物をいかに水平保持するか
それが最初の課題だった。
「上がダメなら下からやってみたらどうだ」
今度は下からエアーを吹き出す方法にチャレンジした。この頃になると流体に関しての理解もかなり進み、ゆっくり吹き出しても対象物の下に空気膜を形成できることが分かっていた。
しかし、問題は浮いた物体のバランスである。少しでも空気の当たる角度や力が変われば、すぐにバランスが崩れてしまう。そうなれば、落ちて割れるか、互いに接触して破損するか、いずれにしても不良品だ。
「最初の課題はいかにしてワークを水平に保つかだった」
当時、非接触搬送装置の開発に取り組んだ平川信二(品質保証部グループ長)はそう振り返る。
穴の口径・形状を変えたり、材質も様々なものを使ってみた。金属も試したが、年数が経てば錆が出る可能性があると指摘され止めた。
まさにトライ&ドゥの連続だった。エアーの吹き出し口も口径を大きくしたり小さくしたり色々試してみた。
一般的には口径が大きいほど吹き出すエアーの速度は遅くなる。だが、それでは空気膜が出来にくい。それよりは小さな穴を無数に開けた方が空気膜が出来やすい。そこで選ばれたのがセラミックスだった。
セラミックスは多孔質素材で、内部にミクロン単位の穴が無数に空いている。しかも穴の方向は一定方向ではない。いわばアットランダムに様々な方向へ穴が空いているわけで、そのことがかえって好都合だった。
早速、波佐見焼きで有名な長崎県波佐見町の窯業試験場に協力を依頼し、地元の窯元を紹介してもらう。
「先方も大変だったと思いますよ。セラミックスといってもいままでは皿や器などのオールドセラミックスを作っていた窯元ですから。工業用セラミックス関係の仕事はしたことがなかったと思います。
材質にしてもいままでとは違って、ゴミが出ないきれいな材質を使ってもらわなければなりませんから、まずそこから入りました」
と平川は語る。
ゴミ、といってもミクロン単位の塵埃だが、不純物が混ざっていればセラミックスの中をエアーが通過する時に、それらがゴミとしてクリーンルーム内に舞い上がる。そのため検査は厳密の上にも厳密に行われ、検査用のエアーもメーカーからクリーンなものを購入して使ったほどだ。
(文中敬称略)
|