「クリーンルームで動かせるリフトを」
ユーザーの一言が開発につながった。
2度目のチャンスは90年に幕張メッセで開催された東京国際物流展の会場でやって来た。
「クリーンルーム内で動かせるリフトが作れないか」
高速で稼働するハイリフターの様子をじっと見ていたソニーの社員が、近付いてくるなりそう言った。
それまでリフトはゴミを撒き散らすためクリーンルーム内では一切使われてなかった。そのため一回一回外に出して、エレベーターで上げ、さらにクリーンシャワーを浴びてという煩わしい工程を採らざるをえない。もし、クリーンルーム内で稼働するクリーンなリフトがあれば、作業工程が短縮され生産性が格段にアップすることになる。高速で昇降するリフトを作れるぐらいだから、クリーンルーム内で稼働するリフトも作れないか、と言うのだ。
「やりましょう」
そう返事をしたものの、クリーンルームなど見たこともない世界である。最速リフターを開発した時とは随分勝手が違った。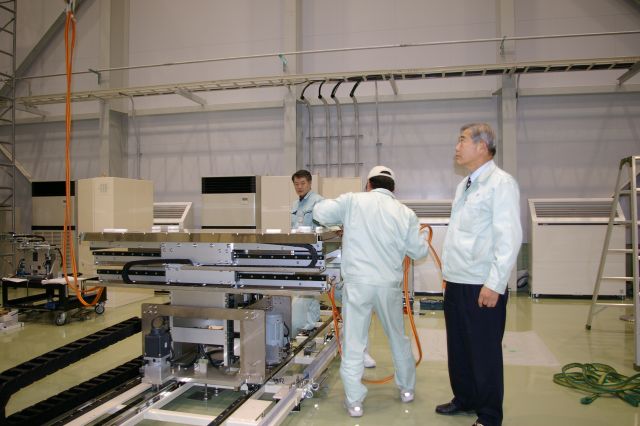
「今度はミクロン単位のゴミとの戦いですからね。いままで我々が経験したことがないことにチャレンジするわけでしょ。それは開発チームには随分苦労をかけましたよ」
と篠原は当時を振り返る。
「苦労したのはクリーンを維持することでした。最初はとにかくクリーンにしなければいけないということで、すべてクリーンなものを使いました。例えば材質も鉄ではなくステンレスを使うなど、装置全体をクリーンにしようとしたんです。そうするとコストがかかりすぎる。それでソニーさんからもアドバイスをもらい、製品を扱う領域のみクリーン度を高めるミニエンバイロメント方式を採用しました。1号機は我々が開発したというより、ソニーさんから色々アドバイスを頂きながら開発したという感じでしたね」
と平川。
91年11月、クリーンルーム内で稼働するクリーンなリフトが完成した。開発には当初の予定の倍以上を費やし、5カ月のところが1年かかった。
クリーンルームで稼働するクリーンなリフトということから「クリフター」と名付けられた1号機は、ソニーの厚木工場に納入された。「いまでも稼働しているはずです」と平川は言う。
クリフター開発のニュースは瞬く間に業界で噂になり、翌月、幕張メッセで開催されたセミコン・ジャパン91にクリフターを出展すると、同社のブースには人だかりが出来た。話題性だけではなかった。各社ともアップする一方のクリーンルームの運転コスト低減に頭を痛めていたからだ。それだけ「クリフター」の開発は待ち望まれていた。
「横がダメなら、立てて運べないか」
逆転の発想で開発した革命的な新装置
年が明けると、篠原は半導体関連業界への本格的な参入を決意し、クリーンルームの建設に着手した。
建設費約2億円の設備投資に不安がなかったわけではない。シリコンサイクルと言われるように半導体業界は過去4年に1度の周期で好況・不況が繰り返されていることは分かっていた。しかし、中長期的に見た場合、高い成長率で伸びている市場なのも間違いなかった。
前進するためにはクリーンルームの建設は絶対必要だ。
篠原はそう判断した。
92年10月、福岡県粕屋郡新宮町(後に本社も同地に移転)に待望のクリーンルームが完成した。もう前に進むしかない。篠原は改めて決意を固めた。それから6年後の98年10月、非接触搬送装置「MAGIC MOVE」が世に出た。
だが、篠原はそれで満足しなかった。彼の目はまだその先を見ていた。
「ウェハーやガラス基板はますます大型化している。それに対応して搬送システムも大型化せざるをえないし、工場用地はますます大きくなっていく。そうなると建設コストも運転コストもアップしていくだけではなく、国内には建設用地がなくなる。なんとか省スペースで、より高速搬送できる装置が作れないだろうか」
そう考えていた。
液晶パネルの素材となるガラス基板の製造が開始されたのが1991年。第1世代と呼ばれた当時のサイズは320mm×400mm。その後、第2、3、4と続き、ことしからは第7世代が主流になると見られている。その間にガラス基板のサイズはどんどん大型化していき、第7世代のサイズは1870mm×2200mm。わずか10数年の間に面積比で33倍強になっている。
このまま大型化が進めば、篠原が言うように早晩建設用地は国内はもとより地球上からなくなるかもしれない。では、どうすれば工場の省スペース化ができるのか。
篠原はここでも独創的なアイデアを出した。
「横ではなく縦にしたらどうだろう」
いままでごく当たり前に行われていた水平搬送という常識を疑ったのだ。たしかに縦にすればスペースは劇的に縮まる。だが、縦にした基板をどこで支えるのか。いわゆる支持点をどこに、どのように作り、運ぶのかが問題だ。
「垂直に立てようとするから難しいので、斜めに立てて運べばいいんですよ」
と、こともなげに言う。
垂直から傾斜角度15度〜20度斜めに傾けたまま搬送しようとしたのだ。支持点の問題は水平搬送の時に開発した非接触を利用した。サイドの支持部分からエアーを吹き出して押し上げながら運ぶのだ。
「こういう方法があったのか。これは気付かなかった」
非接触縦型搬送システムを目にした大見忠弘は地声の太い声をさらに太くして感嘆した。
この時以来、大見は折に触れ、「福岡に第一施設工業というすごい会社がある」と宣伝している。
(文中敬称略)
|